Mechanical Asset Integrity
Unrivaled Dedication to Ensuring Operational Efficiency
Nondestructive Testing (NDT) is essential for maintaining safety, integrity, and reliability in various structures and systems. It evaluates material properties and detects flaws without damaging or altering functionality, preventing accidents, reducing downtime, and extending equipment service life. NDT contributes to cost savings and sustainability by minimizing repairs, replacements, and resource waste. The effectiveness of traditional NDT depends on the expertise of each technician.
Turnkey Data Management Solutions
NVI’s Project Management and Engineering Department is supported by a team of certified API Inspectors, SNT TC-1A Level II NDT Technicians, AutoCAD Operators and Data Management Specialists, allowing us to provide holistic solutions. NVI’s data management team has experience in all major internal data management systems (IDMS), such as AWARE, PSAIM, PCMS with RBI Module, VisualAIM, UltraPipe, as well as NVI’s own IDMS and NVIsion.
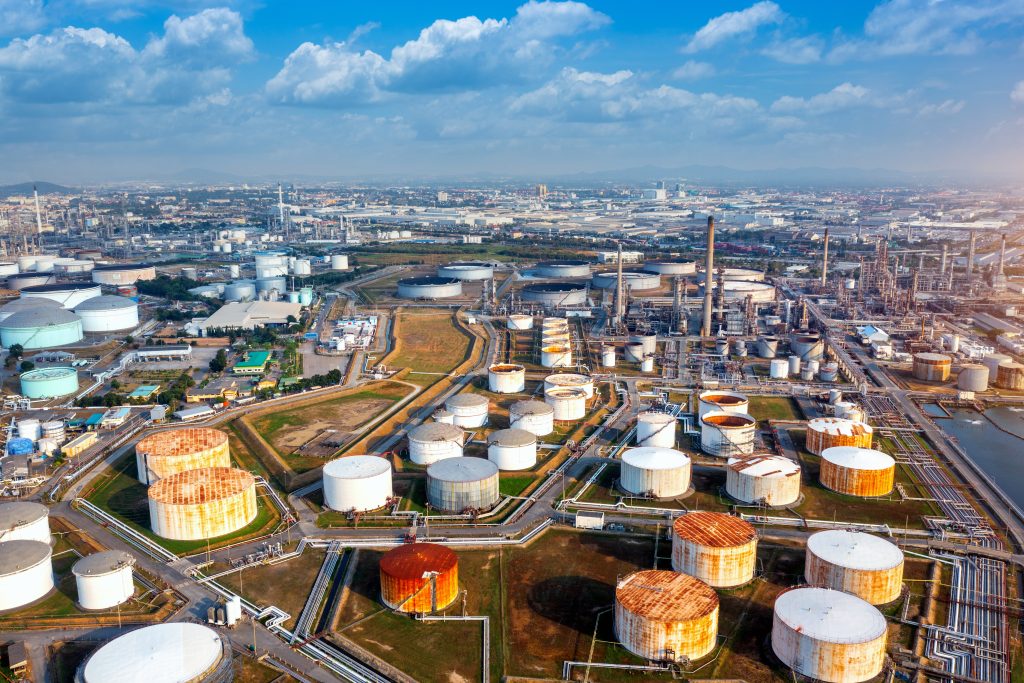
Service Offerings
- API 580 / 581 – Risk-Based Inspection
- API 650 – Welded Tanks for Oil Storage
- API 579 – Fitness-For-Service evaluations
- API 510- Pressure Vessel Inspection
- API 570 – Process Piping Inspection
- API 653 – Above Ground Storage Tanks
- API 936 and NACE Coatings and Refractory
- STI SP001 – Steel Tank Institute
- Visual Testing (SNT-TC-1A)
- Infrared Thermography
- Corrosion – Under Insulation
- External Corrosion Inspections
- Integrity Management
- Regulatory Inspections
- Rope Access Inspections
- Data Management
- PMI (XRF, LIBS, OES)
- NACE Coating Inspection
- Certified Welding Inspector (CWI)
- Leak Test / Hydro Test Documentation
- NACE Cathodic Protection
(surveys, anode installations) - Tank Inspections
- Eddy Current / Remote Field
- Short / Long (MSS) Guided Wave
- Automated UT (AUT) – A, B & C Scan
- Hardness Testing
- Electro Spark Testing
- Video Probe / Borescope Internal Inspection
About
Conventional NDE
NVI has more than 100 SNT-TC-1A Level II radiographers, ultrasonic shear wave technicians, magnetic particle inspectors, and dye penetrant technicians. They are certified or accepted by a wide range of governing bodies, including DNV, ABS, IBS, Lloyds, PED, NOV, API, AWS, and ASME.
API 580 & 581 Risk-Based Inspection
NVI conducts these inspections to determine both the probability and consequences of failure, establish inspection intervals, ascertain the extent of the inspection required, and determine the most suitable type of nondestructive evaluation to use. Our technicians typically draw on their knowledge of risk assessment, risk mitigation, risk acceptance, and risk communications.
API 579 Fitness-for-Service Evaluations
NVI performs these quantitative engineering evaluations to demonstrate the structural integrity of an in-service component that may contain a flaw or be damaged. Our goal is to determine the component’s remaining life, possible methods of remediation, and required in-service monitoring.
API 510 Pressure Vessel Inspection
API 510 covers internal and external inspection, rerate, repair, and alterations to in-service pressure vessels and their associated pressure-relieving devices. External visual inspections, conducted by an NVI-certified 510 inspector or an examiner qualified to perform an external inspection, covers the outside surface of a vessel, insulation condition, paint/coating condition, supports, associated structures, leaks hot spots, vibration and allowance for expansion and alignment of the vessel on its supports. Internal visual inspections can be conducted only by certified 510 inspectors. They are performed to locate damaged areas on the internal pressure boundary surfaces that could not be found during an external inspection.
API 570 Process Piping Inspection
Performed by an NVI API 570 inspector or trained examiner, API 570 covers inspection, rerate, repair, and alterations to in-service process piping and their associated pressure relieving devices. These inspections are conducted to confirm the external condition of the piping and the integrity of the insulation, painting/coating, and associated components. They should reveal signs of misalignment, vibrations, and leaks.
API 653 Above Ground Storage Tank
NVI maintains trained API 653 inspectors on staff for external inspections, which cover the condition of the foundation, coating condition, insulation condition, conditions of tank appurtenances, leaks, distortion, and settlement. Internal inspections focus on ensuring that there is no severe corrosion or leaks in the tank floor.
Code Compliance Inspections
NVI serves customers by providing inspections that meet code requirements for each component. The inspections we offer include API 510 for pressure vessels, API 570 for piping, and API 653 for tank inspection, repair, alteration, and reconstruction.
Corrosion-Under Insulation
Thanks to NVI’s corrosion-under insulation program, clients can operate with the confidence of knowing their equipment is in sound working order. Our specially trained technicians will choose the most appropriate approach—whether visual inspection, guided longwave, radiography, or installation of inspection ports—according to circumstances.
External Corrosion Inspections
Visual inspection is the most commonly used method to identify external corrosion, through tools such as guided longwave can be used for inaccessible areas. Once the areas are identified, specially trained NVI technicians evaluate the area in light of all relevant code requirements.
Internal Corrosion Inspections
NVI technicians will use ultrasound, radiography, or guided longwave technologies to identify suspected areas of internal corrosion, and then employ B-scan or C-scan to map out those areas in detail.
Integrity Management
NVI will work with clients to develop and perform cost-effective integrity management services that comply with BSEE, SEMS, and PSHA 1910 requirements. NVI’s integrity management inspections reduce downtime and ensure the safety and environmental performance of onshore and offshore facilities.
Regulatory Inspections
As a ISO 9001:2008-certified company, NVI performs inspections that meet requirements set forth in the Code of Federal Regulations by agencies such as the Nuclear Regulatory Commission (NRC), the Occupational Safety and Health Administration (OSHA), the U.S. Department of Transportation, and the Pipeline and Hazardous Materials Safety Administration (PHMSA).
Rope Access Inspections
NVI employs SPRAT-certified Level I, II, and III rope access technicians for projects that would otherwise require scaffolding. They typically conduct ultrasonic, radiographic, magnetic particle, dye penetrant, and visual inspections, but can also use guided wave, phased array, and corrosion mapping technologies. NVI can also use rope access to conduct NACE-compliant paint and coating inspections.
Data Management
The Asset Integrity Division of NVI utilizes the team approach to a comprehensive solution based inspection program of your assets has proven to be very successful. Our clients are provided with the most accurate analysis possible. The data is then organized in a customized, cost-effective report created for ease of analysis, review, and scheduling of follow-up inspections and implementation of programs that meet regulatory requirements of OSHA and API recommended best practices.
Our vast experience in the field has been nationally recognized by significant operators and independents. The Asset Integrity team is believed to be the best team of API-Certified Inspectors, Certified ASNT NDE Inspectors, computer specialist, and Auto-CAD operators in the industry.
Customized Software for Data Analysis, UltraPipe, PSAIM, AutoCAD, Web-based Report Viewing/Tracking
PMI
NVI uses PMI for chemical analysis of welding consumables. These tests often form the basis of materials traceability reports for fabrication clients who have purchased stock material or wish to identify materials in inventory.
X-Ray Fluorescent – When a material is bombarded with high-energy X-rays, each constituent element emits characteristic secondary X-rays. These secondary emissions can be measured, revealing the percentage of each element present. The advantage of this technology is that it is portable and quick. X-ray fluorescence is a convenient system – the equipment can be contained in a handheld gun – but it cannot measure carbon content. It is, however, an excellent option for alloyed steels.
Optical Emission Spectroscopy – At NVI, this is the technique of choice for analyzing high-carbon steels. This technique can identify every element on the periodic table, but it requires a large, bulky machine. The spectroscope generates an electric arc and computes the composition of metal by measuring the characteristic light intensity that elements produce when they are heated.
NACE Coating Inspection
NVI employs a team of Coating Inspection Personnel holding Level I, II, and III certifications in NACE’s recognized Coating Inspection Program (CIP) and its Pipeline Corrosion Integrity Management (PCIM).
Certified Welding Inspector (CWI)
NVI’s certified welding inspectors set the stage for successful welds. They work with our customers to make sure that certified procedures have been established and tested for the materials and consumable using destructive testing methods. They then train and test welders to make sure they follow the procedure exactly when they go out in the field. Our certified welding inspectors have passed the American Welding Society examination, indicating that they are extremely knowledgeable about welding and that they can produce the highest level of quality workmanship.
Leak Test/Hyrdo Test Documentation
Hydrostatic testing is a way to test a component for strength and leaks. A pressure vessel or piping system is filled with a liquid, most commonly water, and pressurized with air to hold the pressure of 125% of its Maximum Allowable Working Pressure. This process provides adequate proof that the allowable working pressure is safe for operations. We have individuals trained to witness this testing procedure and provide a quality formal report from the tests to satisfy the client’s needs.
Video Probe/Borescope Internal Inspection
The borescope is a small flexible tube with a small camera attached to one end of the tube connected to a visual aid on the other. Using this instrument, we can perform visual inspections on the internals of piping systems and pressure vessels that a person cannot physically access.
Visual Testing (ASNT-TC 1A)
NVI – certified welding inspectors can represent our clients in the field, visually inspecting all welds before they are subject to nondestructive testing. They can determine if the weld is penetrated if the material is adhering to both sides and if all the relevant dimensions are adhered to. Certified welding inspectors can also serve as the client’s representative during welding and testing, ensuring the job is conducted in a safe, carefully coordinated manner and that all materials are accounted for.
Infrared Thermography
NVI uses the latest infrared technology to pinpoint hot spots in metals or plastics on components such as wellheads, piping, piston engines, turbines, and compressors. Infrared thermography produces visual images that allow temperatures to be compared over a broad area and detects deteriorating components facing high-temperature locations that before they fail. Infrared thermography is a sound alternative for inaccessible or hazardous locations.
NACE Cathodic Protection
Cathodic protection controls the corrosion of metal surfaces by effectively turning them into the cathode of an electrochemical cell. The technician connects a sacrificial metal, which serves as an anode, to the objects – for instance, a tank or length of piping needing protection. The sacrificial metal anode will corrode before the protected element begins to deteriorate.
Surveys – NVI provides close internal routine inspections for cathodic protection integrity. These inspections meet or exceed API 651 criteria. We perform cathodic protection surveys in onshore and offshore environments (often while performing topside inspections). They are conducted by technicians specially trained to evaluate anode conditions and who are knowledgeable about anode installations. As part of the inspection, we will produce detailed drawings of well sites that identify anode locations.
Anode Installations – NVI employes specialized personnel trained to properly dig and install anodes while preserving the integrity of multiple types of equipment. As a matter of policy, NVI always contacts a states’ “one-call” service before an installation.
Level I Topside – NVI performs full visual surveys in compliance with all NACE regulations.
Level II & III Meeting API RP 2A – NVI’s Level II & Level III surveys include flooded member, cathodic protection potential on platforms and risers, anode inspection and installation, visual riser inspection, magnetic particle inspection, and structure damage inspection.
Tank Inspections
Here at NVI, we have experienced and highly qualified API 653 inspectors and NDE technicians.
Our out-of-service and in-service tank reports are designed to be concise, yet comprehensive, and include evaluations following API Standard 653, NDE data, and engineered repair recommendations. Industry and application-specific visual inspectors are available for your project and can be mobilized throughout the United States.
MFL Floor Scanners – The Magnetic Flux Leakage (MFL) system, is a method of nondestructive testing used to detect corrosion and pitting most commonly on the floor sections of above ground tanks. A powerful magnet is used to magnetize the floor of the tank. In areas where corrosion, pitting, dents, or in some cases, cracks are present, the magnetic field “leaks” from the steel allowing us to identify the suspect areas accurately. We can then present a detailed report to the client showing the areas in need of repair or replacement.
Vacuum Box – Vacuum Box testing is one of the safest and reliable nondestructive test methods. This method can locate leaks in a test area that cannot be directly pressurized. The test is performed by spraying a detergent (soap) based solution on an area, placing the vacuum box over said area, and creating a vacuum in the area that the solution was sprayed. If a leak is present in the testing area, the detergent solution will start to bubble.
Robotic Crawlers – By using the latest technology with robotic crawlers, it allows us to inspect areas that were previously inaccessible by other means. Using high power magnets, the crawlers can travel up the sides of the tank to gather thickness measurements. The crawlers can also travel around the circumference of the vessel to gather readings. The crawlers can also be used to scan an area of a vessel. We have two types of crawlers. We have an automatic crawler to an extendable pole that the technician can manually slide up the sides of the tanks.
API 653 Inspection – NVI maintains trained API 653 inspectors on staff for external inspections, which cover the condition of the foundation, coating condition, insulation condition, and conditions of tank appurtenances, leaks, distortion, and settlement. Internal inspections focus on ensuring that there is no severe corrosion or leaks in the tank floor.
Settlement Surveys – Settlement Surveys are performed to ensure that a storage tank remains level during its operations. Elevation measurements are taken around the tank to ensure that there isn’t any tilting or sinking present. The settlement surveys focus not only on the shell side of the tanks, but the floors of the tanks are inspected as well to ensure that there isn’t any settlement that could affect the integrity of the tank by causing leaks, cracks, or buckling of the tank floor. Each survey is performed to the satisfaction of API 653.
Eddy Current
Eddy Current equipment can be used for a variety of applications such as the detection of cracks (discontinuities), measurement of metal thickness, and the measurement of electrical conductivity and magnetic permeability. At NVI, we use eddy current inspection because it is an excellent method for detecting surface and near-surface defects when the probable defect location and orientation are well-known.
Guided Wave (GUL)
Guided Ultrasonic Long-Range testing is used to scan a large volume of pipe to detect areas that may have some metal loss. To identify the problem areas, a transducer and a collar are placed around the pipe. The transducer, controlled by a computer, will shoot low-frequency sound waves 360 degrees around the pipe wall and down the pipe in both directions from the source. This remotely operated screening technique is used to identify damage mechanisms occurring both internally and externally such as leaks, corrosion, erosion, cracks, dents, etc. Once a flaw is discovered, it is recorded. This method allows for a reduction in overall inspection and insulation costs. NVI uses it to inspect inaccessible areas such as road crossing as well as for straight runs of pipe over long distances. It is approved by the Pipeline and Hazardous Materials Safety Administration.
Automated Ultrasonic Testing (AUT)
Automated Ultrasonic Testing is a method that uses scanners that travel around the weld to indicate and map out the location, size, and shape of the present flaws or corrosion areas. While the scanner is in motion, the scans become visible on a computer inside of the truck for review on the spot. NVI used automated systems to test components while they are in service. They can be accomplished using crawlers, robotic vehicles, or track systems. The advantages of this technology include speed, accuracy, and broad area coverage.
A, B, & C Scan
Hardness Testing
Hardness measurements are widely used for quality control of materials because they are quick and considered to be nondestructive test when the marks or indentations produced by the test are in low-stress areas. NVI uses a large variety of methods used for determining the hardness of a substance. A few of the more common methods are Brinell, Rockwell, and Vickers.
Electro Spark Testing
Electro spark testing is most commonly used to detect voids where a coating fails to bond to the underlying material. These voids, or holidays, often cannot be seen visually. Technicians pass the electro spark tester along the surface, producing a series of electrical pulses. If there is a holiday, the pulse generates a spark at its precise location. Electro spark testing is often used to inspect the interior of a vessel.
What Shapes
Our Expertise
We strive to deliver the gold standard in customer satisfaction by standing behind our people and equipment to ensure the job gets “Done Right.”